The 10-Year Legacy of the Deadly Rana Plaza Collapse
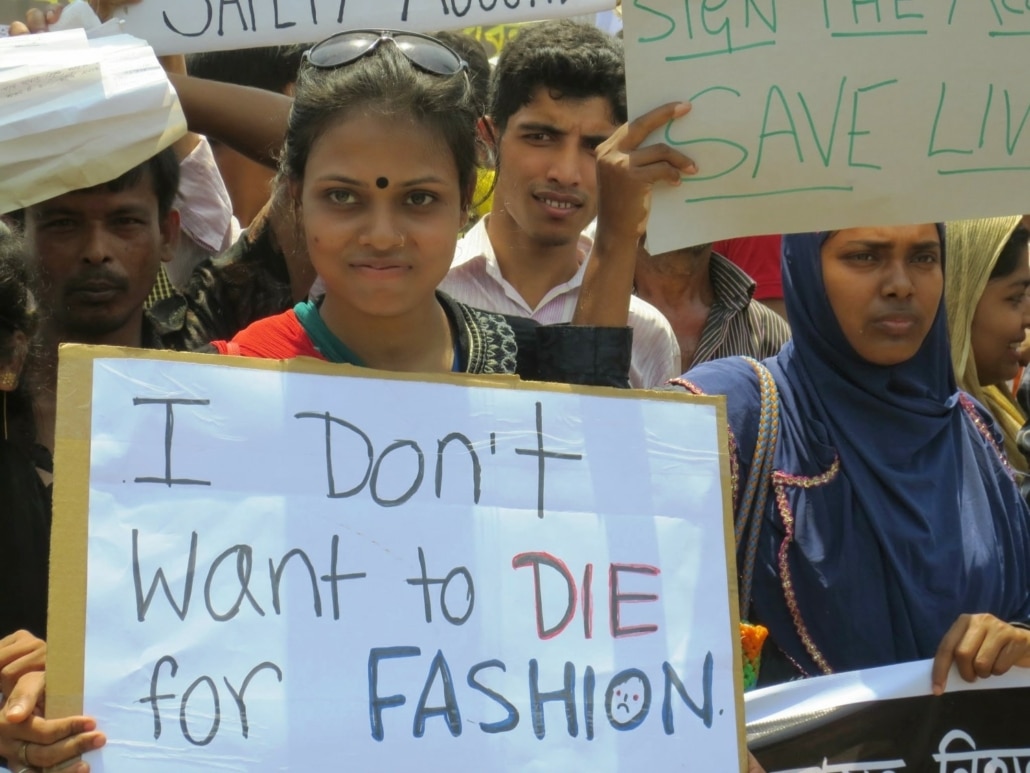
The haunting images of Rana Plaza are still seared in our consciousness. In the worst industrial accident since Bhopal, the collapse in 2013 of the clothing factory complex outside of Dhaka, Bangladesh, killed more than 1,100 workers, mostly young women, and injured another 2,500. Poorly constructed and weakened by the vibrations of a two-ton generator on the roof, the eight-story building had visible, growing cracks in its walls about which workers had warned their supervisors the day before the collapse. The workers were told they would lose their jobs if they refused to return, so they went back the following morning. Many ended up beneath the rubble.
Ten years later, the anniversary of the Rana Plaza disaster offers an opportunity to reflect on the progress that has been made and the work that still needs to be done to ensure decent conditions for Bangladesh’s more than four million garment workers.
With more than 165 million people, Bangladesh is the eighth-most-populous country in the world. It has a land mass of roughly 57,000 square miles, slightly larger than the state of Iowa, making it among the most densely populated countries in the world. It also is a country with significant economic, social, climate-related challenges. Despite producing only 0.56 percent of global emissions, Bangladesh is the seventh-most-vulnerable country to climate devastation, according to Germanwatch’s 2021 Global Climate Risk Index (CRI). A 2018 U.S. government report found that 90 million Bangladeshis, more than half the population, live in “high-climate exposure areas.” It has been estimated that by 2050, one in every seven people in Bangladesh will be displaced by climate change.
Despite the environmental dangers it faces, the country, in some respects, has experienced remarkable progress. When Bangladesh gained independence from Pakistan in 1971, 80 percent of its people lived below the poverty line. Today that percentage stands at 20 percent, including about 6 percent who live in extreme poverty. The dramatic growth of the garment sector has been key to the country’s economic growth and poverty reduction. In 1984, when the Bangladesh Garment Manufacturers and Exporters Association (BGMEA) began keeping records, there were 384 garment factories employing just over 120,000 workers. Today, there are an estimated 7000 factories, most producing at least some products for export. In 2021-22 export income tied to the apparel industry was over $42 billion, making it the second-largest garment exporting country in the world, after only China. This sector accounts for more than 80 percent of all export income for Bangladesh.
After the Rana Plaza collapse, products made for a number of prominent global brands like The Children’s Place, Joe Fresh, Benetton, and Mango, and major retailers like Walmart, were found buried under the rubble. These and other global companies organized two unprecedented collective efforts to address factory-safety issues across the industry. In the absence of adequate government oversight, more than 200 mostly European brands and retailers, including H&M, Inditex (Zara), and Primark, along with major European unions, created the Accord for Fire and Building Safety. A similar collective effort called the Alliance for Bangladesh Worker Safety was organized by about 20 mostly U.S. brands, including Walmart, Target, and the Gap. Under these separate pacts, major international buyers agreed to pay for factory inspections of about 2,500 factories. The inspections identified corrective actions factory owners needed to undertake, at their expense, if they wanted to continue to do business with foreign brands and retailers.
Subscribe to the Ethical Systems newsletter
As a result of these efforts, manufacturing facilities were structurally reinforced and exits were made more accessible. Factory owners installed more fire alarms, sprinklers, extinguishers, and fire doors. Because of these improvements, factory safety has improved significantly over the last 10 years, especially for the larger factories with direct ties to Western corporate buyers. Today, Bangladesh also has some of the greenest factories in the world. All of these are important accomplishments, reflecting sustained collective action by buyers, suppliers, unions, and civil society organizations.
On the negative side, relationships between Bangladeshi factory owners and their corporate customers, which were badly strained by the Covid pandemic, have continued to squeeze the factory owners, and this exploitation leads to worse conditions for workers, who have little power to protect their own wellbeing. Last week, the NYU Center for Business and Human Rights, which I direct, published a report titled, “A Broken Partnership: How Clothing Brands Exploit Suppliers and Harm Workers—And What Can be Done About it.”
Written by Natasja Sheriff Wells and Chana Rosenthal, it describes exploitative practices that buyers applied during the pandemic which have become the new normal with respect to purchasing practices. These include brands pressuring suppliers to make unreasonable price reductions; delaying deliveries and withholding payments; canceling bookings and projections, which leaves manufacturers with unused capacity and raw materials; and using third-party intermediaries to place added pressure on suppliers.
The Center’s report urges increased transparency and communication between global buyers and their local suppliers and a more collaborative business partnership that allows local manufacturers to make reasonable profits while also extending better pay and benefits to their workers. Today, the minimum wage in Bangladesh is the equivalent of about $75 dollars a month, a number that has dropped by more than 20 percent because of the depreciation in recent years of the local currency, the taka. The increased cost-cutting pressures coming from global buyers has worsened this downward spiral.
As we reflect on the anniversary of Rana Plaza, the most important reform going forward will be to fix this broken partnership and to build a more responsible system for global outsourcing. In Bangladesh and elsewhere, global fashion brands need to accept their share of the responsibility for ensuring the well-being of factory workers whose labor is a crucial component of the continued growth and vitality of this industry.
Michael Posner is the Jerome Kohlberg professor of ethics and finance at NYU Stern School of Business and director of the Center for Business and Human Rights. Follow him on Twitter @mikehposner.
Lead image: Solidarity Center / Flickr
Reprinted with permission from Forbes.